Motor Bloğu Neden Çatlar ?
28-06-2025
22:45
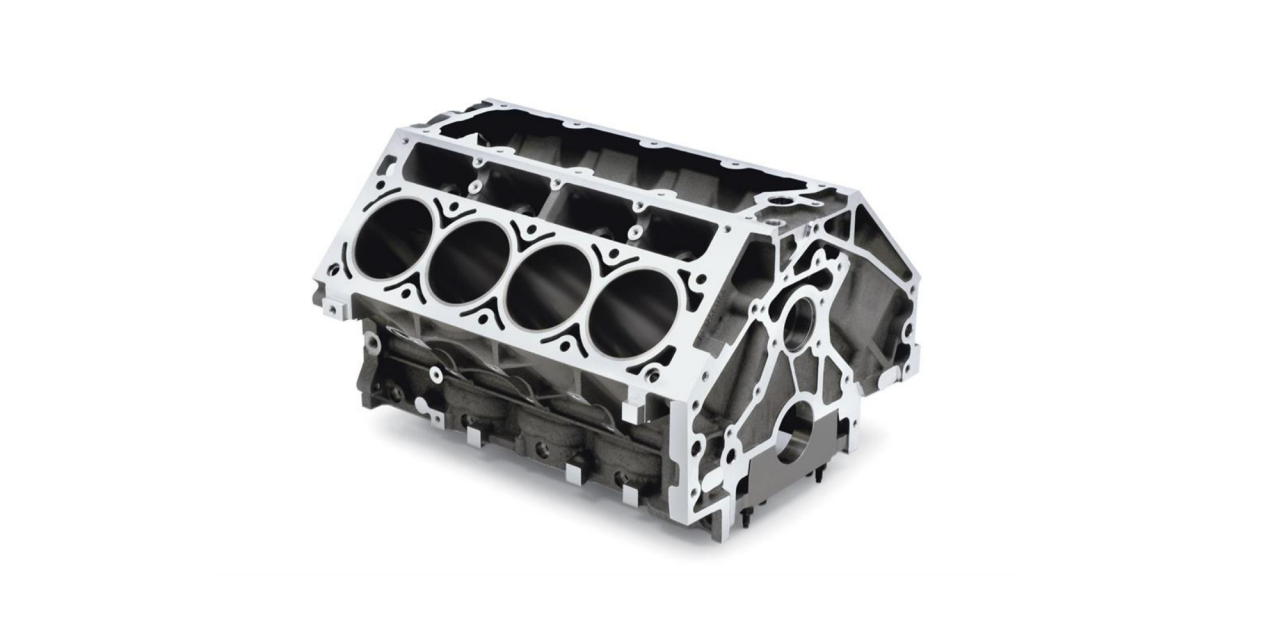
Motor Bloğu Nedir?
Motor bloğu, içten yanmalı motorların temel yapı taşlarından biridir ve kritik bir bileşendir. Genellikle dökme demir veya alüminyum alaşımlarından imal edilen motor bloğu, silindirleri barındırdığı gibi, yağ kanalları, soğutma yolları ve montaj noktaları da içerir. Motor bloğu, silindirlerin yerleşimini sağlarken, hareketli parçaların uyumlu çalışmasına imkan tanır. Motorun genel verimliliği üzerinde belirleyici bir etkiye sahiptir.Motor bloğunun tasarımı, motorun performansı ve dayanıklılığı üzerinde doğrudan etkili olduğu için mühendislik açısından son derece önemli bir konudur. Silindir dizilimi, bloğun hacmi ve soğutma özellikleri gibi faktörler, motor güç üretimi ve yakıt verimliliği üzerinde belirleyici olmaktadır. Ayrıca, motor bloğunun sıcaklık toleransı, yani ısınmaya karşı gösterdiği direnç, motordaki çatlakların ve deformasyonların önlenmesinde kritik bir rol oynar. Düzgün işlev gören bir motor bloğu, motorun genel ömrünü uzatarak, hem performansı artırır hem de onarım masraflarını en aza indirir.
Bununla birlikte, motor bloğu, sürekli olarak mekanik ve termal streslere maruz kalmaktadır. Zamanla, malzeme yorgunluğu ve aşınma gibi problemler ortaya çıkabilir, bu da çatlakların oluşmasına neden olabilir. Özellikle sıcaklık dalgalanmaları ve yüksek basınç koşullarında, motor bloğundaki yapısal bütünlük zayıflayabilir. Bu durum, motorun çalışmasını tehdit ederken, aynı zamanda motor bloğunun çeşitli parçalarının değişim gerekliliğini de beraberinde getirebilir. Bu bağlamda, motor bloğunun hem tasarım sürecinde hem de kullanım aşamasında dikkatli bir şekilde izlenmesi ve bakıma tabi tutulması, motorun uzun ömürlü ve verimli çalışmasını sağlamak açısından son derece önemlidir.
3. Çatlak Nedenleri
Motor bloğu çatlaklarının oluşumunda çeşitli nedenler etkili olabilir. Bu nedenlerin doğru bir şekilde anlaşılması, motor performansı ve dayanıklılığı açısından kritik öneme sahiptir. İlk olarak, aşırı ısınma başlıca faktörlerden biri olarak öne çıkmaktadır. Motor çalışma sırasında gerekli soğutma sıvısının yetersizliği veya soğutma sistemindeki arızalar, motor bloğunun sıcaklık seviyesinin kabul edilebilir sınırların üzerine çıkmasına yol açabilir. Yüksek sıcaklık altında metalin genişleme ve büzülme özellikleri, malzeme bütünlüğünü tehdit eder ve zamanla çatlakların oluşmasına zemin hazırlar. Bu tür ısıl stres, özellikle motorun sık sık duraklatıldığı ve hızla yeniden çalıştırıldığı durumlarda daha belirgin hale gelir.Diğer bir önemli neden, düşük kalite malzemelerin kullanımıdır. Motor üretiminde kullanılan metal ve alaşımların kalitesi, motorun dayanıklılığını doğrudan etkiler. Uluslararası standartların altında kalan malzeme kullanımı, motor bloğunun yapısal bütünlüğünü zayıflatabilir. Bu bağlamda, düşük kaliteli malzemeler, yeterli mukavemet ve ısıl direnci sergileyemeyerek zamanla yıpranma ve çatlama riskini artırır. Özellikle, gereksinimlere uygun şekilde tasarlanmamış ve test edilmemiş malzemelerin kullanılması, hem üretim sürecinde hem de motorun çalışma ömrü boyunca ciddi sorunlara yol açabilir.
Son olarak, yanlış montaj uygulamaları da motor bloğu çatlaklarına neden olabilir. Motor bileşenlerinin hatalı veya uyumsuz şekilde bir araya getirilmesi, yapısal gerilimlerin dengesiz dağılımına yol açar. Uygun montaj tekniklerinin göz ardı edilmesi, zamanla motor bloğunun kritik bölgelerinde zayıflığa ve çatlakların tedrici olarak gelişmesine neden olabilir. Yanlış sıvı dolum seviyeleri veya montaj işlemleri sırasında yanlış torq değerlerinin kullanılması gibi faktörler de bu süreci hızlandırır. Motor bloğu çatlaklarına yol açan bu nedenlerin anlaşılması, hem mevcut sorunların çözümünde hem de gelecekteki motor tasarımı süreçlerinde dikkatle değerlendirilmelidir.
3.1. Aşırı Isınma
Aşırı ısınma, motor blok çatlaklarının meydana gelmesindeki temel nedenlerden biri olarak karşımıza çıkmaktadır. Motorların çalışma sıcaklığı, optimal performans ve dayanıklılık açısından kritik bir öneme sahiptir; zira anormal derecede yükselen sıcaklıklar, motor bloğu ve diğer bileşenlerde yapısal deformasyonlara yol açabilir. Motorun içindeki yanma süreci, yüksek sıcaklıklar ve basınçlar yaratırken, soğutma sisteminin yetersiz kalması durumunda bu sıcaklıkların daha da yükselmesi kaçınılmazdır. Aşırı ısınmanın başlıca sebepleri arasında soğutma sıvısının yetersizliği, termostat arızaları, su pompasının işlevini yerine getirememesi ve motor yağının viskozitesinin düşmesi sayılabilir.Motorun aşırı ısınması, uzun dönemde malzeme yorgunluğuna ve buna bağlı olarak çatlak oluşumuna zemin hazırlar. Örneğin, alüminyum bloklar, yüksek ısılar altında malzeme özelliklerini kaybederek deformasyona uğrayabilir. Bu, motorun radyatöründe, soğutma sysletime ve silindir kapaklarında ciddi hasarlara yol açar. Kısacası, yüksek ısılar altında motor bloğunda çatlakların gelişme mekanizması, termal genleşme ve darbe gerilmeleri gibi fiziksel prensiplerle doğrudan ilişkilidir. İşte bu nedenle, motorun çalışma sıcaklıklarını dikkatle izlemek ve gerekli önlemleri almak, uzun ömürlü bir motor performansı için kritik bir unsur teşkil etmektedir.
Son olarak, aşırı ısınmaya neden olan süreçlerin doğru bir biçimde tespit edilmesi, motor arızalarının önlenmesi ve bakım stratejilerinin geliştirilmesi açısından da son derece önemlidir. İşletme koşulları, aracın yaşadığı iklim koşulları ve sürücü davranışları gibi faktörler, aşırı ısınma riskini etkileyen unsurlar olarak değerlendirilmeli; motor sisteminin bütünlüğünü sağlamak adına proaktif bir yaklaşım benimsenmelidir. Motor bloğu çatlaklarının önlenmesi için ahtapot stratejisiyle hem yapısal sağlamlığın korunması hem de dinamizmin sürekli izlenmesi, motor verimliliği açısından hayatî bir öneme sahiptir.
3.2. Düşük Kalite Malzeme
Motor bloğu çatlaklarının oluşumu, kullanılan malzeme kalitesine doğrudan bağlıdır. Düşük kalite malzeme, motor bloğunun dayanıklılığını ve performansını olumsuz etkileyen önemli bir faktördür. Genellikle, bu tür malzemeler, uygun termal ve mekanik özelliklere sahip olmadıkları için motorun iç dengelerini bozma riski taşır. Düşük kaliteli alaşım ve plastik bileşimlerin kullanımı, motor bloğunun ısınmasını önemli ölçüde artırabilir. Bunun sonucunda, malzeme yapısında gerilmeler meydana gelerek çatlakların oluşması kolaylaşır. Özellikle, dökme demir ve alüminyum gibi malzemelerde mikro çatlakların ve diğer deformasyonların oluşumu düşük kalite hammadde seçiminde sıkça karşılaşılan bir sorundur.Ayrıca, düşük kalite malzemelerin işlenmesi ve montajı, yapısal bütünlüğü zayıflatabilir. Malzemenin homojenliği ve iç yapısı, motor bloğunun mukavemetini doğrudan etkiler. Uygun standartlara uymayan hammadde, önceden tahmin edilemeyen noktalar üzerinde stres birikmesine yol açar. Bu, motorun çalışması sırasında zamanla daha belirgin hale gelen çatlakların tetikleyicisi olabilir. Ayrıca, düşük kaliteli malzemelerin genellikle daha yüksek oranda üretim hatası içermesi, montaj sürecinde de sorunlara yol açabilir; sonuç olarak, çatlaklar önceden var olan zayıf noktaları daha da belirgin hale getirir.
Sonuç olarak, motor bloğunun dayanıklılığı ve uzun ömürlülüğü açısından malzeme kalitesi kritik bir rol oynar. Kalitesiz malzemelerin kullanımı, sadece anlık performans kaybına yol açmakla kalmaz, aynı zamanda motorun genel güvenilirliğini ve verimliliğini tehdit eder. Bu nedenle, motor üretiminde malzeme seçiminde daha yüksek standartların sağlanması ve daha dikkatli bir denetim sürecinin izlenmesi, motor bloğu çatlaklarının önlenmesi açısından kilit bir öneme sahiptir. Elde edilen bilgiler, motor tasarım ve üretim süreçlerinde daha kaliteli malzeme bileşenlerinin tercih edilmesinin gerekliliğini vurgular ve böylece motor ömrünü artırmayı sağlar.
3.3. Yanlış Montaj
Yanlış montaj, motor bloğu çatlaklarının ortaya çıkmasının kritik bir nedeni olarak öne çıkmaktadır. Montaj süreci, motorun dayanıklılığı ve genel performansı açısından son derece önemlidir. Montaj sırasında dikkate alınması gereken birçok faktör bulunmakta olup, bu faktörlerin göz ardı edilmesi, motorun yapı bütünlüğünü tehdit eden çatlaklara yol açabilir. İlk olarak, bileşenlerin doğru hizalanmaması, aşırı mekanik stres yaratabilir. Örneğin, silindir başlığı ile motor bloğu arasındaki bağlantının hatalı yapılması, kayar hareketler ve aşırı sıcaklık değişimlerine neden olabilir; bu da çatlakların oluşumunu hızlandırabilir.Montaj aşamasında kullanılan torq değerlerinin yanlış ayarlanması da bu sorunun önemli bir parçasıdır. Bileşenlerin yanlış sıkıştırılması, hem sızdırmazlık sorunlarına hem de uzun vadede motorun yaslanma noktalarında deformasyonlara yol açacaktır. Şayet bir motor parçası, önerilen tork değerlerine göre sıkıştırılmazsa, malzeme daha fazla gerilmeye maruz kalır ve kırılganlık artırabilir. Bu durum, motor bloğunda mikro çatlakların oluşumuna neden olabilir ve zamanla bu çatlaklar daha büyük hasarlara dönüşebilir.
Son olarak, motorun montajı sırasında dikkatsizlik ya da yetersiz bilgi birikimi de önemli bir etkendir. Eğitim eksiklikleri, mekanik sistemlerin ve bileşenlerin gereklilikleri hakkında yanlış bir algı oluşturabilir. Bu da motorun montajı sırasında hem malzeme seçiminde hem de uygulama tekniğinde hatalara yol açar. Özetle, yanlış montaj, sadece motorun anlık performansını değil, aynı zamanda uzun vadeli dayanıklılığını ve güvenilirliğini de ciddi şekilde tehlikeye atmaktadır. Bu sebeple, montaj sürecinin titizlikle yürütülmesi ve gerekli standartların belirgin bir şekilde uygulanması, motor bloğu çatlaklarının önlenmesinde kritik bir başarı faktörüdür.
4. Motor Bloğu Çatlağının Belirtileri
Motor bloğu çatlaklarının tespiti, motor sağlığının değerlendirilmesi açısından kritik bir aşamadır. Bu çatlaklar, genellikle görünür olmasa da, belirli belirtilerin varlığıyla tespit edilebilir. İlk olarak, sıvı kaçakları, motor bloğunda çatlakların en yaygın işareti olarak öne çıkar. Motor sıvıları, özellikle soğutma sıvısı veya yağ, çatlaklar aracılığıyla sızabilir, bu da motorun alt kısmında oluşan lekeler veya damlalarla kendini gösterir. Bu tür sıvı kaçakları, motorun normal çalışma koşullarını olumsuz yönde etkileyerek aşırı ısınma ve yetersiz yağlama gibi sorunlara yol açabilir. Dolayısıyla, motor bloğu çatlakları, öncelikle sıvı kaçaklarıyla kendini gösterebilir.Motor performansında düşüş de, çatlakların varlığının bir diğer önemli göstergesi olarak dikkat çeker. Çatlak, motor silindirleri arasında basınç kaybına neden olabilir, sonuç olarak motorun verimliliğini düşürerek güç kaybına yol açar. Bu durum, genellikle hızda bir azalma, daha yavaş hızlanma veya motorun düzensiz çalışması şeklinde hissedilir. Kaza anlarında motorun aniden durması gibi acil durumlar yaşanabilir, bu da hem güvenliği tehdit eden hem de onarım masraflarını artıran bir durumdur. Bu nedenle, motor performansında yaşanan anormallikler, soğutma sisteminin aşırı sıcaklık üretmesi ve daha geniş bir mekanik hasarın öncüsü olabilir.
Ayrıca, aşırı ısı, motor bloğu çatlaklarının varlığını dolaylı olarak işaret eden bir başka belirtidir. Motorun normal çalışma sıcaklığının üzerinde ısınması, birçok faktörden kaynaklansa da, çatlakların varlığı ciddi bir rol oynar. Çatlaklar, soğutma sıvısının akışını kısıtlayarak, motorda sıcak hava birikmesine sebep olabilir. Bu durum, motorun aşırı ısınmasına ve muhtemel yanmalara yol açarak, ciddi bir hasar oluşturabilir. Böyle bir durumu önlemek adına, motorun sıcaklık göstergeleri düzenli olarak kontrol edilmeli ve olası belirtiler derhal ele alınmalıdır. Motor bloğu çatlaklarının belirtilerinin zamanında tespiti, araç sahiplerinin büyük onarım masraflarını ve motor kaybını önlemeleri açısından kritik bir öneme sahiptir.
4.1. Sıvı Kaçağı
Sıvı kaçakları, motor bloğunda meydana gelen çatlakların en belirgin ve yaygın belirtilerinden biridir. Bu tür kaçaklar, motorun düzgün çalışmasını tehdit eden birçok sorunun temel kaynağını oluşturabilir. Motor soğutma sıvısı, yağ ya da diğer sıvılar, çatlaklar aracılığıyla dışarı sızdığında, motorun verimli işleyişi engellenir. Sıvı kaçakları, genellikle motorun temel yapısında aşınma veya darbe sonucu oluşan çatlaklar ile ilişkilidir. Ayrıca, motor bloğundaki otorite hareketleri zayıfladıkça, bu çatlaklar zamanla genişleyebilir ve daha büyük sorunlara yol açabilir.Sıvı kaçağının tespiti, motorun durumunu değerlendirmek açısından kritik öneme sahiptir. Kaçak genellikle, motor bloğu yüzeyinde soğutma sıvısı veya yağ birikintilerine yol açarak görsel olarak belirlenebilir. Ancak, belirli sıvıların kaybolması hemen fark edilmese de, motor üzerindeki sıcaklık değişimleri ve performans düşüşleri bu durumun ayırt edici işaretleridir. Özellikle, soğutma sıvısının kaybı, motorda aşırı ısınma riskini artırdığı için, bu durum daha da önem kazanmaktadır. Motorun yeterli derecede soğutulamadığı durumlarda, iç bileşenlerde aşınma ve yıpranma hızlanabilir, bu da motorun uzun ömürlülüğünü ve güvenilirliğini tehdit edebilir.
Kaçak saptandığında, motor bileşenlerinin incelenmesi ve gerektiğinde onarımlar yapılması hayati öneme sahiptir. Herhangi bir kaçak belirtileri gözlemlendiğinde, motorun güvenli bir biçimde durdurulması ve bir uzmana danışılması önerilmektedir. Erken teşhis, sadece motor arızasının önlenmesine değil, aynı zamanda maliyetleri etkili bir şekilde azaltmaya da katkı sağlar. Sıvı kaçaklarının neden olduğu hasarları minimize etmek, daha kapsamlı arızaların önüne geçmek amacıyla stratejik bir yaklaşım geliştirilmesini gerektirir; bu da motor bloğu çatlakları ile mücadelede önemli bir adımdır.
4.2. Motor Performansında Düşüş
Motor performansında düşüş, araçların verimliliği üzerinde olumsuz etkiler yaratan karmaşık bir durumdur. Genellikle, motor bloğu çatlakları ile ilişkilendirilebilecek bu performans kaybı, farklı faktörlerden kaynaklanabilir. Çatlaklar, motor soğutma sıvısının yanma odasına sızmasına veya egzoz gazlarının silindirlere kaçmasına neden olabilir. Bu durum, motorun içindeki basıncı ve sıcaklığı artırırken, aynı zamanda yağ sirkülasyonunun bozulmasına yol açar. Sonuç olarak, motorun genel verimliliği düşerken, yakıt tüketimi artar ve egzoz emisyonları da yükselir. Tüm bu etkiler, motorun performansını doğrudan etkilediğinden, dikkatle incelenmelidir.Motor performansındaki düşüş, genellikle aşamalı bir süreçtir. Başlangıç aşamasında, düşük güç üretebilir, titreşimler artabilir ve motorun normal işleyişi bozulmaya başlayabilir. Araç sahibi bu tür belirtileri gözlemlediğinde, genellikle motorun performansı ile ilgili bir sorun olduğunu anlayabilir. Uzun süreli ihmal, daha ciddi durumlara yol açarak, motorun daha fazla zarar görmesine ve onarım maliyetlerinin artmasına neden olabilir. Dolayısıyla, motor performansında yaşanan azalma, anında müdahale gerektirir.
Çatlakların belirlenmesi ve motor performansındaki düşüşün düzeltilmesi için, titiz bir denetim sürecinin uygulanması esastır. Bu süreç, motorun detaylı bir şekilde incelenmesini, mevcut sorunların teşhis edilmesini ve uygun tamir yöntemlerinin devreye alınmasını içerir. Ayrıca, motorun performansını iyileştirmek için düzenli bakım ve kontrollerin yapılması, motorun ömrünü uzatırken, olası sorunların önüne geçme şansı sunar. Mesleki litelere dayalı inceleme ve testler, motor bloğu çatlaklarının belirlenmesi ve motor performansını artırmada kritik bir rol oynar. Bu tür bir sistematik yaklaşım, yalnızca motor verimliliğinin artırılmasıyla kalmaz, aynı zamanda araç sahibi için de uzun vadeli avantajlar sağlar.
4.3. Aşırı Isı
Aşırı ısı, motor bloğunun sağlığı için kritiktir ve motor çatlaklarının belirlenmesine dair önemli bir gösterge sunar. Motorun çalışması esnasında, belirli bir sıcaklık aralığında faaliyet göstermesi kritik olup, bu sıcaklık aralığının aşılması, motorun çeşitli bileşenlerinde daimi hasarlara yol açabilir. Aşırı ısı, genellikle motorun soğutma sistemiyle ilgili yetersizlikler, yağ eksikliği veya yanma odasındaki anormallikler gibi çeşitli nedenlerden kaynaklanır. Özellikle, motor bloğu ve silindir kapakları arasındaki ısı transferinin bozulması, bölgesel aşınmalara ve sonuç olarak çatlak oluşumuna zemin hazırlayabilir.Aşırı ısının motor üzerindeki etkileri oldukça fazladır. İlk aşamada, motorun malzemesi olan alüminyum ve çelik gibi metalleri zayıflatması, yapısal bütünlüğü tehdit eder. Uzun süreli aşırı ısıya maruz kalma, malzemelerin genleşmesine ve yerel deformasyonlara yol açabilir. Ayrıca, silindirler arasında sıcaklık dengesizliği, yanma verimliliğini düşürerek motor performansında kayıplara neden olur. Aşırı ısı giderici sistemlerin yetersiz kalması, motorun genel çalışma koşullarını olumsuz etkileyerek, aşırı ısınmanın belirgin semptomlarının ortaya çıkmasına sebep olur; bu semptomlar arasında motorun genellikle normalden çok daha yüksek sıcaklıklara ulaşması, garip seslerin duyulması ve motor sıvılarında bozulmalar sayılabilir.
Motor bloğundaki çatlakları tespit etmek için alevle kontrol veya termal görüntüleme gibi yöntemler kullanılabilir. Bu tür yöntemler, motorun aşırı ısıya maruz kalıp kalmadığını analiz etmekte oldukça etkilidir. Termal görüntüleme, motorun aşırı ısınmış bölgelerini hızlı bir şekilde belirlerken, alevle kontrol ise belirli bölgelere odaklanarak çatlak oluşumunu ortaya çıkarabilir. Dolayısıyla, aşırı ısının motor bloğuna etkileri ve çatlakların tespiti, motor performansının sürekliliğini sağlamak adına dikkate alınması gereken kritik unsurlardır. Motor tarihçesi, bakım kayıtları ve anlık sıcaklık takibi, yani bu parametrelerin izlenmesi, motor sağlığını olumlu etkileyerek potansiyel sorunları erken aşamada tespit etmeyi kolaylaştırır.
5. Görsel Muayene Yöntemleri
Görsel muayene yöntemleri, motor bloğu çatlaklarının tespitinde temel bir öneme sahiptir. Bu yöntemler, motorun genel durumunu değerlendirmek ve olası yapısal kusurları ortaya çıkarmak için sıklıkla kullanılır. Görsel muayenenin ilk aşaması, yüzey kontrolüdür. Yüzey kontrolü sırasında, çatlakların ve diğer anormalliklerin görünür olduğu yerler dikkatlice incelenir. Bu süreç, motor bloklarının dış yüzeyindeki bozulmaların varlığını belirlemek için sistematik bir yaklaşım gerektirir. Genellikle, yüksek kaliteli bir aydınlatma ve büyütme ekipmanları kullanılarak yüzeydeki çatlaklar, çizikler ve diğer hasarlar net bir biçimde gözlemlenir. Yüzey kontrolü uygulaması, hem görsel hem de deneysel incelemelerle bütünleştirilerek, belirli bölgelerde daha derin incelemeleri de tetikleyebilir.Renk değişimi de görsel muayene metotlarından bir diğer önemli unsurdur. Motor bloğu üzerindeki renk değişimi, materialin gerilime maruz kaldığını gösterebilecek bir işarettir. Özellikle, yüksek sıcaklıklara ve termal şoklara maruz kalan metal yüzeylerde bu tür değişiklikler belirginleşir. Sıcaklık dalgalanmaları nedeniyle oluşan ısı etkileri, metalin yapısında hasar yaratabilir ve zamanla çatlakların meydana gelmesine neden olabilir. Renk değişikliklerinin incelenmesi, görülemeyen çatlakların ve deformasyonların varlığını gün yüzüne çıkarabilir. Bu aşamada, detaylı bir inceleme yapılırken, gözlemlenen değişimlerin motor sağlığı üzerindeki potansiyel etkileri de dikkate alınmalıdır. Görsel muayene yöntemleri, genellikle non-destructive test (NDT) yöntemleriyle birleştirildiğinde, daha güvenilir ve kapsamlı bir sonuç elde edilmesine katkıda bulunur, bu da motor bloğunun uzun ömürlü ve performans açısından verimli olmasını sağlar.
5.1. Yüzey Kontrolü
Yüzey kontrolü, motor bloğu çatlaklarının belirlenmesi sürecinde kritik bir aşamadır. Bu işlem, doğrudan gözlemlere ve fiziksel muayenelere dayalıdır, bu sayede yüzeydeki potansiyel hasar kaynakları hızlı ve etkili bir şekilde tespit edilebilir. Motor bloğundaki çatlaklar genellikle, aşırı sıcaklık değişimleri, sürekli mekanik stres ve malzeme yorgunluğu sonucu ortaya çıkarak, motor performansını olumsuz etkileyebilir. Bu bağlamda, yüzey kontrolü sırasında odaklanılması gereken unsurlar arasında çatlakların konumu, boyutu ve yönü yer alır.Görsel muayene işlemi, yeterli aydınlatma ve uygun gözlem açılarının sağlanması ile başlar. Yüzeydeki her türlü pürüzlülüğün, sıyrığın veya çatlağın belirlenmesi için dikkatli bir inceleme gerçekleştirilmelidir. Özellikle, çatlakların içeriye doğru derinleşebileceği varsayımı ile yüzeyden kaçış yollarının (örneğin, sıvıların motor bloğunun iç kısmına sızma riski) değerlendirilmesi gerekmektedir. Kullanılan ekipmanın kalitesi de bu aşamanın başarısını etkileyebilir. Örneğin, güçlü bir el dürbünü veya mikroskop kullanarak gözlemlenen çatlakların belirginliği artırılabilir. Bunun yanı sıra, yüzey kontrolünde ultrasonik testler gibi yardımcı yöntemler de devreye girebilir. Bu teknikler, gözle görülmeyen iç çatlakların tespitini kolaylaştırır ve muayene sürecini daha kapsamlı hale getirir.
Yüzey kontrolü sırasında elde edilen bulgular, daha ayrıntılı muayeneler ve onarımlar için değerli bir temel sağlar. Tespit edilen çatlakların genişliği ve büyümesi, motorun genel durumu hakkında önemli bilgiler sunar. Dolayısıyla, gözlemler yalnızca motor bloğunun mevcut durumunu yansıtmakla kalmayıp, gelecekteki bakım ve onarım stratejileri için de yol göstericidir. Bu süreçte kayıt tutma ve verilerin analitik bir şekilde değerlendirilmesi, uzun vadede motor performansını artırmak ve olası arızaları en aza indirmek adına büyük önem taşımaktadır. Bu nedenle, yüzey kontrolü, motor bloğu çatlaklarının belirlenmesi aşamasında vazgeçilmez bir unsurdur, mekanik sistemlerin sürekliliği ve verimliliği açısından kritik bir rol oynamaktadır.
5.2. Renk Değişimi
Renk değişimi, motor bloğu çatlaklarının belirlenmesinde kritik bir görsel muayene yöntemi olarak öne çıkmaktadır. Bu yöntem, malzeme üzerinde gözle görülür bir renk değişikliğinin varlığını tespit etmeye odaklanır ve böylece içsel hasarların veya çatlakların varlığını dolaylı bir şekilde işaret eder. Genellikle, metal yüzeylerde meydana gelen renk değişimleri, malzemenin fiziksel bütünlüğünde bir bozulma, aşınma veya kimyasal etkileşim sonucu oluşan mikro çatlakların bir belirtisi olarak değerlendirilir. Özellikle motor blokları, yüksek sıcaklıklara maruz kalmaları nedeniyle, zamanla termal stres ve oksidasyon gibi faktörlerden etkilenebilir. Bu durum, metalin yüzey özelliklerini değiştirebilir ve belirgin renk tonları ortaya çıkabilir.Renk değişimlerinin doğru bir şekilde değerlendirilmesi, uzmanların motor bloğunun mevcut durumunu belirlemelerinde önemli bir rol oynar. Örneğin, motor bloğunun üst kısmındaki koyu lekeler veya anomaliler, antifriz sızıntıları veya yanık kalıntıları gibi sorunları işaret edebilir. Renk değişimlerinin gözlemlenmesi, sadece yüzeydeki sorunları değil, aynı zamanda iç mekanizma üzerindeki potansiyel tehditleri de ortaya koyabilir. Dolayısıyla, renk değerlendirmesi sırasında dikkat edilen noktalar arasında renk tonu, yoğunluğu ve dağılım haritası gibi faktörler bulunur; bu durum, uzmanların hangi bölümlerin daha fazla hasar gördüğünü veya hangi alanlarda bakım gerçekleştirilmesi gerektiğini netleştirmelerine yardımcı olur.
Renk değişimi inceleme yönteminin etkinliği, diğer muayene teknikleriyle birleştirildiğinde, estetik gözlemlerle birleşen sistematik bir yaklaşım sunar. Bu tür entegre bir inceleme, motor bloğu üzerinde derinlemesine bir analiz yaparak, potansiyel çatlakların doğrudan tespit edilmesinin yanı sıra, bu çatlakların olası nedenleri ve sonuçları hakkında da bilgi sağlar. Renk değişimi, dolayısıyla, motor performansı ve güvenliği açısından kritik bir unsur haline gelir ve bakıma yönelik stratejilerin yönetilmesinde temel bir belirleme aracı işlevi görür.
6. Sesli Muayene Yöntemleri
Sesli muayene yöntemleri, motor bloğu çatlaklarının tespiti için önemli bir non-destrüktif test olarak öne çıkmaktadır. Bu yöntem, motor çalışırken ortaya çıkan seslerin dikkatlice analizi ile, anormal durumların saptanmasına olanak tanır. Motorun iç dinamikleri sırasında kaçınılmaz olarak meydana gelen sesler, mekanik arızaların ya da aşınma durumlarının göstergesi olabilmektedir. Seslerin dinlenmesi ve analizi, dikkate alınması gereken temel noktaları belirlemek için kritik öneme sahiptir.Anormal sesler, motorun çalışan parçaları arasında uygunsuz bir durumun meydana geldiğini işaret eden önemli bir işarettir. Örneğin, çatlakların sebep olduğu sesler genellikle yüksek frekanslı tıslama, vurma veya gıcırtı şeklinde kendini gösterir. Bu tür seslerin varlığı, motor bloğunun bütünlüğünün tehdit altında olduğuna ve potansiyel bir arıza riskinin bulunduğuna işaret eder. Dolayısıyla, motorun ses dinamikleri, uzman teknisyenler tarafından titizlikle analiz edilmelidir. Bu seslerin kaynağının doğru belirlenmesi, motorun ileride daha ciddi arızalardan korunmasına yardımcı olabilir.
Sesli muayene, genellikle ekipman yardımıyla gerçekleştirilse de, deneyimli bir teknisyenin işitme tecrübesi büyük bir avantaj sağlar. Teknologlar, anormal seslerin kayıt altında tutulması ve daha sonra analiz edilmesi için çeşitli ekipmanlar kullanabilir. Böylece, ses örnekleri karşılaştırılarak motor içerisindeki potansiyel çatlaklar net bir biçimde tespit edilebilir. Bu yöntemin uygulamadaki etkinliği, titiz bir ses analitiği ile pekiştirilmekte, seslerin zamanla nasıl değiştiğini anlamaya yardımcı olmaktadır. Genel olarak bakıldığında, sesli muayene yöntemleri, motor bloğu analizinde vazgeçilmez bir aracıdır ve düzenli yapıldığında, motorun ömrünü uzatma ve güvenilirliğini artırma konusunda önemli rol oynamaktadır.
6.1. Anormal Sesler
Motor bloğu çatlaklarının tespiti, araçların güvenli ve verimli çalışabilmesi açısından kritik bir öneme sahiptir. Bu bağlamda, anormal seslerin tespiti, motor bloğundaki potansiyel sorunların anlaşılmasına yardımcı olan etkili bir sesli muayene yöntemi olarak öne çıkmaktadır. Motor çalışırken duyulan sesler, yalnızca aracın genel sağlığına dair ipuçları sunmakla kalmaz; aynı zamanda belirli bileşenlerin durumunu da yansıtabilir. Örneğin, normal koşullarda seslerin hafif ve düzenli olması beklenirken, tahrip olmuş veya çatlak motor blokları, vurma, tıslama ya da metal sürtünmesi gibi olağandışı sesler üretebilir.Anormal seslerin kaynağını belirlemek, çeşitli faktörlerin dikkatlice analiz edilmesini gerektirir. Seslerin frekansı, tonu ve süresi gibi unsurlar, olası sorunların teşhisi için önemli ipuçları sağlar. Örneğin, yüksek frekanslı tıslama sesleri, genellikle motor yağlama sisteminin yetersizliğine veya piston halkalarının aşınmasına işaret edebilirken, düşük frekanslı vurma sesleri, su pompası veya krank milinin bozulmuş olabileceğini gösterebilir. Bu nedenle, motorun çalışma döngüsündeki düzenlilik ve sesin doğası dikkatle izlenmelidir. Ayrıca, seslerin yanında gelen titreşimler de önemli bir gösterge olabilir; aşırı titreşimler, motor bloğunda meydana gelen yapısal hasarların belirtisi olabilir.
Sesli muayene yöntemleri, sadece anormal seslerin tanımlanmasında değil, aynı zamanda bu seslerin zaman içindeki evrimini izlemekte de faydalıdır. Yılda yapılan periyodik kontroller sırasında anormal seslerin tespit edilmesi, kritik arızaların önlenmesine katkı sağlayabilir. Günlük kullanım sırasında dinleme alışkanlığı geliştirilmesi, kullanıcıların bu tür sesleri erken safhalarda tanımasına olanak tanır. Dolayısıyla, motor bloklarında meydana gelen çatlakların belirlenmesinde ses analizi, hem ekonomik hem de güvenlik boyutları açısından büyük önem taşır. Motor performansının sürdürülebilirliği ve aracın güvenli bir şekilde çalışması için bu tür seslerin dikkate alınması, profesyonel bakım süreçlerinin önemli bir parçası haline gelmiştir.
7. Basınç Testi
Basınç testi, motor bloğundaki çatlakların ve diğer yapısal bütünlük sorunlarının tespit edilmesinde kritik bir araçtır. Bu yöntem, motorun çalışma sırasında maruz kaldığı sıcaklık ve basınç koşullarını simüle ederek, özellikle sızdırmazlık problemlerinin belirlenmesine olanak tanır. Test süreci genellikle motor bloğunun hermetik bir sistem içerisinde kapatılmasıyla başlar. Ardından, belirli bir basınç seviyesine ulaşmak için bir gaz ya da sıvı kullanılır. Basınç uygulandıktan sonra, sistemin belirli bölümlerindeki olası sızıntılar, basıncın düşmesi veya dışarıda görülen sıvı veya gaz çıkışı ile tespit edilir. Motor bloğundaki çatlaklar genellikle gözle görülmeyen ve sadece basıncın artmasıyla açığa çıkan sorunlardır. Bu nedenle, basınç testinin dikkatlice ve sistematik bir şekilde yapılması büyük önem taşır.Sıkıştırma testi, basınç testinin bir alt kümesi olarak, motorun silindirlerinin ve yakıt sisteminin bütünlüğünü değerlendirmek için uygulanır. Bu test, silindirler arasındaki sıkıştırma oranlarını kontrol ederek, herhangi bir sızdırmazlık kaybını veya iç sızıntıyı tespit eder. Motor çalışırken meydana gelecek herhangi bir sıkıştırma kaybı, motorun verimliliğini olumsuz yönde etkileyebilir. Dolayısıyla sıkıştırma testleri, genellikle motorun bakımından önce veya sonrasında yapılarak, motorun genel sağlığının değerlendirilmesine yardımcı olur.
Soğutma sıvısı basıncı, motor bloğuna karşı uygulanan başka bir basınç testi türüdür. Bu test, motorun aşırı ısınmasını önlemek ve soğutma sisteminin etkinliğini sağlamak amacıyla gerçekleştirilir. Soğutma sıvısı basıncı test edilirken, sistemdeki basınç seviyeleri belirlenir ve soğutma sıvısının uygun bir seviyeye ulaşıp ulaşmadığı kontrol edilir. Soğutma sıvısındaki basınç kaybı, sistemdeki potansiyel çatlakları veya sızdırmazlık problemlerini gösterir. Bu nedenle, soğutma sıvısı basıncı testi, motorun performansının sürdürülebilirliğini sağlamak için hayati öneme sahiptir. Her iki test türü de motor bloğu çatlaklarının tespiti ve önlenmesinde kritik rol oynamaktadır, bu nedenle motor bakımı sürecinin ayrılmaz parçalarıdır.
7.1. Sıkıştırma Testi
Sıkıştırma testi, motor bloğundaki çatlakların belirlenmesinde kritik bir rol oynamaktadır. Bu test, motor silindirleri içindeki sıkıştırma basıncını ölçerek, motorun genel sağlığı ve verimliliği hakkında önemli bilgiler sunar. Motorun içindeki hava-yakıt karışımının düzgün bir şekilde sıkıştırılması, motorun optimum performansı için gereklidir. Bunun yanı sıra, silindirler arasında hava kaçağı olup olmadığını tespit etmek, motorun güç kaybı ve yanma verimliliği açısından hayati öneme sahiptir. Çatlaklar ya da aşınmalar, silindirin sızdırmazlığını bozarak, sıkıştırma oranını azaltabilir; bu durum da dolaylı yoldan motorun performansını olumsuz etkiler.Sıkıştırma testi, genellikle motorun çalışma sıcaklığında gerçekleştirilirken, çeşitli aletler kullanılarak basınç ölçümleri alınır. Bu işlem sırasında, motorun her bir silindiri sırayla test edilir. İlk olarak, buji veya enjektör yerleri kapatılır, ardından silindirin içine bir test cihazı vasıtasıyla hava gönderilir. Ölçülen basınç, belirli bir standart aralığında değilse, bu durum silindirin içinde bir çatlak veya sızdırmazlık problemi olabileceğinin göstergesi olarak değerlendirilmektedir. Test sırasında, her silindirin ölçümlenen basınç değerleri karşılaştırılarak, tutarsızlık gösteren silindirler belirlenir. Bu, motor bloğundaki problemleri lokalize etmek için oldukça etkili bir yöntemdir.
Test sonuçları, motorun durumu hakkında kapsamlı bir analiz sunar. Elde edilen verilerin yorumlanması, motorun iyileştirilmesi gereken alanlarını ve potansiyel bakım gereksinimlerini ortaya koyar. Dizel ve benzinli motorlar arasındaki sıkıştırma değerlerinin farklılık göstermesi nedeniyle, bu testin motor tipine göre spesifik değer aralıklarıyla değerlendirilmesi gereklidir. Sonuç olarak, sıkıştırma testi, motor bloğu çatlaklarının tespiti açısından sadece bir test değil, aynı zamanda motor performansını etkileyen çeşitli faktörlerin analizini sağlayan bir süreçtir. Bu süreç, motor verimliliğini artırmak ve olası hataları önceden belirleyerek, onarıma olan ihtiyacı minimuma indirmek açısından son derece önemlidir.
7.2. Soğutma Sıvısı Basıncı
Soğutma sıvısı basıncı, motor bloğu çatlaklarının belirlenmesi ve genel motor sağlığı açısından kritik bir parametredir. Motorun soğutma sistemindeki sıvı basıncı, motorun etkin bir şekilde çalışmasını ve optimum sıcaklık aralığında kalmasını sağlamak amacıyla düzenli olarak izlenmelidir. Basınç, soğutma sıvısının motordaki akışkan dinamiklerini etkileyerek, ısının motor parçalarına dağıtılmasına katkıda bulunur. Normal çalışma koşullarında, soğutma sıvısının basıncı 0.9 ila 1.3 bar arasında olmalıdır. Ancak, basınçta meydana gelen artışlar veya düşüşler, sistemde var olan muhtemel arızaların işaretleri olarak değerlendirilmelidir.Basınç testleri, soğutma sıvısı sisteminin sızdırmazlığını kontrol etmek için yararlı bir yöntemdir. Bu süreçte, motordaki soğutma sistemi kapalı bir devre içerisinde test edilir; böylece herhangi bir sızıntı veya basınç kaybı kolaylıkla tespit edilebilir. Test sırasında, sıvı basıncı belirli bir seviyeye yükseltilir ve sistemin bu basınca dayanıklılığı gözlemlenir. Eğer basınç belirlenen seviyeden düşerse, bu durum, motor bloğunda veya borularda çatlaklar veya hasar olduğunu gösterir. Ayrıca, soğutma sıvısının yeterli seviyede tutulması, gazların içinde birikmemesi ve gereksiz ısınma ile birlikte motordaki olası arızaların önlenmesi açısından da elzemdir.
Soğutma sıvısı basıncının sürekli izlenmesi, motorun genel sağlığı için göz ardı edilemeyecek bir işlem olmasıyla birlikte, zamanında tespit edilen herhangi bir anormallik, ağır aşınma hallerinin ve büyük onarım masraflarının önüne geçer. Motor tasarımlarında entegre edilen otomatik basınç izleyicileri, bu süreci daha da kolaylaştırarak, sürücülere gerçek zamanlı bilgiler sunar. Sonuç olarak, soğutma sıvısı basıncının izlenmesi, hem motor performansının artırılması hem de genel bakım ihtiyaçlarının minimize edilmesi açısından kritik bir öneme sahip, motor bakımının vazgeçilmez parçalarından biridir.
8. Sıvı Kontrolü
Motor bloğundaki çatlakların belirlenmesi, motor sistemlerinin genel verimliliği ve dayanıklılığı açısından kritik bir öneme sahiptir. Bu bağlamda, sıvı kontrolü işlemi, motorun sağlıklı çalışabilmesi için hayati bir aşamadır. Sıvı kontrolü, motor içerisindeki yağ ve soğutma sıvısı seviyelerinin düzenli olarak izlenmesini içerir, bu sayede olası arızaların erken tespit edilmesi sağlanır. Yağ seviyesi, motorun yağlama sisteminin etkili bir şekilde çalışması için gereklidir; çünkü motorun metal parçalarının sürtünmesini azaltarak aşınmayı minimize eder. Yetersiz yağ seviyesi, motorun aşırı ısınmasına ve sonuç olarak ciddi hasarlara yol açabilir. Bu nedenle, yağ seviyesi düzenli aralıklarla kontrol edilmeli, gerektiğinde uygun tipte yağ eklenmeli veya değiştirilmelidir.Öte yandan, soğutma sıvısı seviyesi de benzer şekilde motor bloğunun sağlığı üzerinde doğrudan etkiye sahiptir. Soğutma sıvısı, motorun çalışma sıcaklığını ideal seviyelerde tutarak, ısıya bağlı hasar riskini azaltır. Düşük soğutma sıvısı seviyesi, motorun aşırı ısınmasına yol açarak, silindir kapak contası gibi kritik bileşenlerin hasar görmesine neden olabilir. Bu durum, motorun performansını düşürür ve pahalı onarımlara yol açabilir. Dolayısıyla, soğutma sıvısının düzenli kontrolü ve gerektiğinde, belirlenen standartlar çerçevesinde takviye edilmesi, motorun ömrünü uzatmak ve verimliliğini artırmak açısından oldukça önemlidir.
Sonuç olarak, motor bloğu çatlaklarının tespitinde sıvı kontrolü işlemleri, motor performansını optimize etme ve olası arızaların önüne geçme konusunda büyük bir rol oynar. Bu kontrollerin sistematik olarak yapılması, hem motorun çalışma ömrünü uzatır hem de genel bakım maliyetlerini düşürür. Sıvı seviyelerinin korunaklı ve dikkatli bir şekilde yönetilmesi, motorun aşınmasını azaltarak, genel verimliliği artırır ve mekanik arızaların önlenmesine katkıda bulunur. Dolayısıyla, sıvı kontrolü, motor bakım ve onarım işlemlerinin temel taşlarından biri olarak değerlendirilmektedir.
8.1. Yağ Seviyesi
Yağ seviyesi, motorun sağlıklı çalışabilmesi için kritik bir unsurdur ve motor bloğundaki çatlakların belirlenmesinde dolaylı fakat önemli bir rol oynar. Motor yağları, hem soğutma hem de yağlama işlevi görebilen özel maddelerden oluşur ve bu özellikleri dolayısıyla motorun performansını doğrudan etkiler. Yetersiz yağ seviyesi, sürtünmeyi artırarak motor parçalarının aşınmasına neden olabilir; bu durum, motor bloğunda çatlıkların ortaya çıkma riskini artırır. Üreticiler, motor yağ seviyesinin düzenli olarak kontrol edilmesini ve optimal seviyede tutulmasını önerir; çünkü yağın yalnızca içeriği değil, aynı zamanda seviyesi de motorun genel sağlık durumu hakkında önemli ipuçları verir.Yağ seviyesinin kontrolü, çoğu motorlu aracın bakım rutininde yer alır ve genellikle periyodik olarak gerçekleştirilmesi gereken bir işlemdir. Genellikle araç sahası içinde yer alan yağ dip çubuğu ile kolayca ölçülebilen yağ seviyesi, motorun çalışma verimliliğini etkileyen bir göstergedir. Eğer yağ seviyesi belirtilen aralıkta değilse, bu durum motorun aşırı ısıya maruz kalmasına ve dolayısıyla potansiyel çatlakların oluşumuna zemin hazırlayabilir. Ayrıca, yağın kalitesi ve durumu da göz önünde bulundurulmalıdır; kirlenmiş veya oksitlenmiş yağ, yağlama performansını düşürerek motor bileşenleri üzerinde olumsuz etkiler yaratabilir. Dolayısıyla, yalnızca yağ seviyesinin değil, aynı zamanda yağın performansının periyodik olarak izlenmesi önerilmektedir.
Motor yağ seviyesi, işletme koşullarına göre değişiklik gösterebilir. Özellikle ağır yük taşıyan veya yüksek hızlarda seyahat eden araçlarda yağ seviyesinin daha sık kontrol edilmesi gerekebilir. Motor yağı tüketimi; motorun yaşı, çalışma sıcaklığı ve sızdırmazlık durumu gibi faktörlere bağlı olarak artabilir. Dolayısıyla, yağ seviyesinin düzenli kontrol edilmesi, yalnızca motorun sağlığını korumakla kalmayıp, aynı zamanda olası motor bloğu çatlaklarının önceden belirlenmesine olanak tanır. Bu tür proaktif bakım uygulamaları, hem maliyetleri düşürür hem de motorun ömrünü uzatır, böylelikle araç sahiplerinin uzun vadeli yatırım getirisini artırır.
8.2. Soğutma Sıvısı Seviyesi
Motor bloğundaki çatlakların tespiti, motorun sağlıklı çalışması için kritik öneme sahiptir. Bu bağlamda, soğutma sıvısı seviyesi, motorun ısısını etkili bir şekilde kontrol etme yeteneğinin bir göstergesi olarak öne çıkar. Motor, meydana gelen ısıyı soğutma sıvısı yoluyla dağıtarak aşırı ısınmayı önlerken, soğutma sisteminin doğru çalışması için bu sıvının seviyesinin sürekli olarak kontrol edilmesi gerekir. Yetersiz soğutma sıvısı seviyesi, motorun aşırı ısınmasına, dolayısıyla motor bloğunda çatlakların oluşumuna neden olabilir. Hem motorun uzun ömürlü olması hem de verimli çalışmasının sağlanabilmesi için soğutma sıvısının zamanında eklenmesi ve gerekli kontrollerin yapılması büyük önem taşır.Soğutma sıvısı seviyesinin ideal aralıkta olup olmadığını belirlemenin birkaç yöntemi bulunmaktadır. İlk olarak, motor durduğunda ve ısınmadığında, soğutma sıvısının genişletme deposundaki seviyesini kontrol etmek gerekir. Su, antifriz ve çeşitli katkı maddeleri içeren bu sıvı, genellikle maksimum ve minimum seviyeler arasında olmalıdır. Bu seviyenin altında kalındığında, motorun daha fazla ısınma riski doğuracağı için sıvı seviyesinin tekrar kontrol edilmesi ve gerekirse tamamlanması gereklidir. Bunun yanı sıra, soğutma sisteminde var olan sızıntılar, aşınmalar veya çatlaklar gibi durumların varlığı da göz önünde bulundurulmalıdır. Bu tür durumlar, soğutma sıvısını kaybetmesine ve motorun ciddi şekilde zarar görmesine yol açabilir.
Sadece soğutma sıvısı seviyesini kontrol etmekle kalmamak, aynı zamanda sıvının kalitesine de dikkat etmek hayati önem taşır. Soğutma sıvısının zamanla ısıl özelliklerinin değişmesi, asidik hale gelmesi veya kirlenmesi motor performansını olumsuz yönde etkileyebilir. Bu bağlamda, soğutma sıvısının periyodik olarak değiştirilmesi, motorun sağlığını korumada etkili bir strateji olarak ortaya çıkmaktadır. Dolayısıyla, motor bloğundaki çatlakların belirlenmesi sürecinde soğutma sıvısı seviyesi, yalnızca düz bir ölçüm değil, aynı zamanda motor bakımı için kapsamlı bir değerlendirme aracıdır.
9. Termal Görüntüleme
Termal görüntüleme, motor bloğu çatlaklarının tespiti için devrim niteliğinde bir yöntem sunar. Bu teknoloji, nesnelerin termal enerjilerini algılayarak, yüzey sıcaklık farklılıklarını görsel bir biçimde temsil eder. Motor bloğunda meydana gelen çatlaklar genellikle içten yanmalı motorların aşırı ısınma veya soğutma sıvısı sızıntıları gibi sebeplerle ortaya çıkar; bu durumda bir termal görüntüleme cihazı, motor yüzeyinde ısının eşit dağılmadığını gösteren sıcaklık anormalliklerini gözler önüne serer. Bu tür anormallikler, bir çatlağın varlığını dolaylı olarak işaret eder ve motorun yapısal bütünlüğü hakkında değerli bilgiler sağlayabilir.Termal görüntüleme, öncelikle, bir termal kamera aracılığıyla gerçekleştirilir. Bu kameralar, sıcaklığı doğrudan ölçebilme yetenekleri sayesinde, motor bloğunun yüzeyinde meydana gelen mikroskopik çatlakların tespitinde oldukça etkilidir. Isı, çatlaklar etrafındaki materyalden farklı bir şekilde yayılır ve bu farklılık, termal kameralar aracılığıyla görüntülenebilir. Örneğin, bir motorun çalışması esnasında, sızdırmazlık malzemesinin çatlaması veya parçaların genişlemesi nedeniyle ortaya çıkan ısı farklılıkları, açıkça gözlemlenebilir. Elde edilen termal görüntüler, operatörlere kritik bir durumun belirlenmesine yönelik birçok olasılığı sunar ve aynı zamanda bakım ve onarım süreçlerinin planlanmasında yardımcı olur.
Bu yöntemin avantajları, yalnızca çatlak tespitinin ötesine geçer. Termal görüntüleme, motor bloğunda oluşabilecek diğer yanlışlar ve sorunlarla ilgili bilgiler sunarak kapsamlı bir analiz imkanı tanır. Sıcaklık anormallikleri, yalnızca çatlakların değil, aynı zamanda sızıntıların, aşınmaların ve bileşenlerin genel sağlığı ile ilgili sorunların bulgularını da barındırabilir. Böylece, motorlarda proaktif bakım uygulamaları teşvik ederek, büyük onarım maliyetlerinin önüne geçilmesine yardımcı olur. Sonuç olarak, termal görüntüleme, motor bloğu çatlaklarının belirlenmesi ve genel motor sağlığının korunması için vazgeçilmez bir araçtır.
10. Ultrasonik Test
Ultrasonic testing (UT) is a non-destructive evaluation technique widely employed to identify structural discontinuities in materials, particularly in engine components like motor blocks. This method utilizes high-frequency sound waves transmitted through the material. When these sound waves encounter imperfections such as cracks or voids, they produce distinct reflections that can be measured and analyzed. The primary objective of ultrasonic testing is to achieve a precise assessment of the integrity of motor blocks, ensuring that any potential defects can be detected early, thus preventing catastrophic failures and optimizing safety in automotive applications.The ultrasonic testing process begins with the application of a coupling agent, which enhances the transmission of ultrasonic waves from the transducer into the workpiece. The transducer generates sound waves that propagate through the motor block. As the waves travel through the material, they travel at a specific velocity contingent on the material’s density and elastic properties. Any discontinuities—such as cracks or other flaws—will reflect a portion of these waves back to the transducer. The reflection data is then displayed on a screen, often in the form of a waveform, allowing the technician to interpret the presence and characteristics of any detected defects. The amplitude and time delay of the reflections provide valuable insights into the size and nature of the imperfections, enabling comprehensive analysis of the motor block's condition.
The advantages of ultrasonic testing are manifold. It offers high sensitivity and the ability to detect small to moderate-sized cracks that may not be visible to the naked eye. Furthermore, it possesses depth penetration capabilities, making it suitable for thick-walled components typically found in automotive applications. Compared to other non-destructive testing methods such as radiography or magnetic particle testing, ultrasonic testing is faster, can be performed on-site, and does not involve hazardous materials or radiation exposure. Consequently, ultrasonic testing serves as a critical tool in predictive maintenance strategies, whereby the structural integrity of motor blocks is routinely assessed, ensuring reliability and longevity while significantly reducing the risk of unanticipated engine failures.
11. Dinamometre Testi
Dinamometre testi, motor bloğu çatlaklarının belirlenmesinde kritik bir rol oynamaktadır. Bu test, motordan alınan güç ve tork verilerini ölçerek, motorun genel performansını değerlendirirken olası yapısel sorunları da ortaya çıkarabilir. Dinamometre, bir motorun belirli çalışma koşullarındaki performansını gerçek zamanlı olarak test eder. Bu süreç, motorlar üzerindeki yükü simüle ederek çatlak oluşumunu veya malzeme yorgunluğunun varlığını tespit edebilmek için oldukça değerlidir. Motorun çalışma koşulları altında performansını analiz ederken, uygulanan tork ve devir sayısının gözlemlenmesi, motor bloğundaki potansiyel hasarların veya zayıf noktaların tespitine olanak tanır.Dinamometre testi sırasında, motor çeşitli RPM değerlerinde çalıştırılırken, belirli bir tork aralığında güç çıkışı ölçülür. Böylelikle, motorun güç eğrisi elde edilir ve bu eğri üzerinden motorun verimliliği ve dayanıklılığı hakkında içgörüler sağlanır. Çatlakların varlığı, genellikle motorun sağladığı güç çıktısında anormallikler olarak kendini gösterir; zira çatlaklar, motor bloğunu zayıflatarak yük altında deformasyona yol açabilir. Dinamometre sonuçları, motorun yapısal bütünlüğünün yanı sıra, performans kaybına neden olabilecek herhangi bir mekanik arızanın veya yapısal değişikliğin varlığını da öne çıkarır. Dolayısıyla, motor bloğu çatlaklarının saptanmasında yönelik bu test, hem doğrudan gözlem yoluyla hem de elde edilen güç verileri aracılığıyla güvenilir bir değerlendirme sunar.
Sonuç olarak, dinamometre testi, motor bloğundaki çatlakların belirlenmesinde etkin bir yöntemdir. Motorun çalışma koşullarındaki performansını titizlikle inceleyerek, potansiyel sorunların önceden tespit edilmesine olanak tanır. Otomotiv mühendisliği ve bakım süreçlerinde bu testin entegre edilmesi, motor ömrünü uzatmak, performans kayıplarını en aza indirmek ve güvenilirlik sağlamak açısından hayati bir öneme sahiptir. Motor bloğu çatlaklarının sistematik değerlendirilmesi, hem ekonomi hem de güvenlik açısından sağlıklı bir mühendislik uygulaması olup, dinamometre testinin verimliliği burada belirgin bir avantaj sunar.
12. Motor Bloğu Çatlaklarının Onarımı
Motor bloğu çatlaklarının onarımı, otomotiv mühendisliğinde son derece önemli bir süreçtir; çünkü bu çatlaklar motor performansını ciddi şekilde etkileyebilir ve motorun genel dayanıklılığını zayıflatabilir. İlk olarak, çatlakların yerlerinin ve boyutlarının doğru bir şekilde tespit edilmesi gerekir. Kapsamlı bir inceleme ile çatlaklar belirlenebilir ve böylece onarım sürecine yönelik en uygun yöntemler seçilebilir. Çatlakların onarımında yaygın olarak kullanılan iki yöntem kaynak ve epoksi uygulamalarıdır. Her iki yöntemin de kendine has avantajları ve dezavantajları mevcuttur; bu nedenle seçim yapmadan önce analiz yapılması gereklidir.Kaynak yöntemleri, metal parçaların birleştirilmesi veya onarılması için özellikle etkili bir tekniktir. Bu süreç, çatlaklı motor bloğunun öncelikle uygun bir temizlik işlemine tabi tutulmasıyla başlar. Çatlak bölgesi, kaynak işleminin verimliliğini artırmak amacıyla düzgün bir şekilde temizlenmeli ve hazırlanmalıdır. Ardından, uygun kaynak malzemesi seçilerek, çatlakların doldurulması ve güçlendirilmesi gerçekleştirilecektir. Kaynak işleminin ardından, kaynak dikişinin sağlamlığı ve doğruluğu kontrol edilmelidir. Ancak, kaynak yönteminin yüksek ısılara maruz kalması, motor bloğunun yapısal bütünlüğü üzerinde olumsuz etkiler yaratabileceğinden, bu süreçte dikkatli olunmalıdır.
Epoksi kullanımı, onarım açısından alternatif bir yaklaşım olarak öne çıkmaktadır. Epoksi reçineleri, çatlakları kapatmak için özel olarak formüle edilmiş dayanıklı bileşenlerdir. Bu yöntemin ilk aşaması, sorunlu bölgenin hazırlanması ve epoksinin uygulanması için yüzeyin pürüzsüzleştirilmesidir. Epoksi, uygulandıktan sonra, kimyasal bağların sağlanması için belli bir süre kuruması beklenir. Epoksi yönteminin avantajı, genellikle sıcaklık ve nem gibi çevresel etkilere karşı gösterdiği dirençtir; bu da yüksek performans şartlarında bile kalıcı bir çözüm sunar. Ancak, epoksi kullanımı, çoğu zaman belirli bir sınırlamaya sahip olabileceğinden ve yalnızca belirli çatlak türleri için uygun olduğu için, uzman bir değerlendirme gerektirmektedir. Her iki onarım yönteminin kombinasyonu, motor bloğu onarımında işlevsel bir çözüm sunarak, motorun ömrünü uzatma amacı gütmektedir. O yüzden, hem kaynak hem de epoksi yöntemleri, motor onarımı süreçlerinde dikkatlice değerlendirilmeli ve seçilmelidir.
12.1. Kaynak Yöntemleri
Kaynak yöntemleri, motor bloğu çatlaklarının onarımında sıkça tercih edilen bir tekniktir ve mekanik yapıların dayanıklılığını artırmak, öngörülen performansı sağlamak için kritik bir rol oynamaktadır. Bu yöntem, esasen iki metal parçanın yüksek ısı altında birleştirilmesi sürecini içerir. Bu süreç, kaynak noktaları arasında moleküler bir bağ kurarak metalin dayanıklılığını artırırken, farklı kaynak türleri de içerik ve uygulama genişliğine göre değişiklik gösterebilir. Genellikle, elektrik ark kaynağı, MIG (Metal Inert Gas) ve TIG (Tungsten Inert Gas) kaynak yöntemleri gibi çeşitli teknikler kullanılmaktadır. Her bir yöntemin avantajları ve dezavantajları, malzeme tipine, çatlağın büyüklüğüne ve konumuna bağlı olarak dikkate alınmalıdır.Kaynak süreci boyunca, ısı girişi miktarı ve kaynak hızının dikkatli bir şekilde kontrol edilmesi gereklidir. Aksi takdirde, kaynak bölgesinde deformasyon, çatlak oluşumu veya malzeme bütünlüğünde bozulma gibi istenmeyen sonuçlar ortaya çıkabilir. Özellikle motor bloğundaki çatlaklar, aşırı sıcaklık dalgalanmaları ve mekanik yüklemeler nedeniyle oluşabileceği için, kaynak yapılacak yüzeylerin dikkatlice hazırlanması ve uygun kaynak elektrotlarının seçilmesi oldukça önemlidir. Tanımlanan çatlakların boyut, biçim ve konum olarak incelenmesi, doğru kaynak yönteminin seçilmesi açısından temel bir adımdır. Yüksek sıcaklıkla eritme ve soğuma esnasında metallerin fiziki özelliklerinin değişimi, kaynak sonrası sonuçların öngörülmesi açısından belirleyici olmaktadır.
Son olarak, kaynak sonrası yapılan test ve kontroller, onarımın kalitesini garanti etmek için elzemdir. Kaynak birleştirmesinin dayanıklılığı, genellikle ultrasonik testler veya x-ray ile görüntüleme yöntemleriyle değerlendirilmektedir. Bu, potansiyel zayıf noktaların tespit edilmesine olanak tanırken, motor bloğunun yeniden kullanıma uygun hale getirilmesi açısından güvenilirlik sunmaktadır. Kaynak yöntemleri, motor bloğu çatlaklarının onarımında hem maliyet etkin hem de işlevsel bir çözüm sunarak mekanik sistemlerin güvenilirliğini artırmaktadır.
12.2. Epoksi Kullanımı
Epoksi, motor bloğu çatlaklarının onarımında yaygın olarak kullanılan bir malzeme olup, sağladığı üstün yapısal özellikler sayesinde motorların dayanıklılığını artırır. Epoksi, iki bileşenli bir reçine ve sertleştirici sisteminden oluşur ve kimyasal olarak, termoplastik malzemelerden daha az büzülerek, güçlü yapılar oluşturur. Uygulama sırasında, epoksi bileşenleri genellikle hacimsel olarak bir araya getirilir, ardından, belirli bir süre boyunca kürlenmesi sağlanır. Bu süreç, epoksinin fiziksel ve kimyasal özelliklerini optimize ederken, yapılan onarımların kalitesini artırır.Çatlakların onarımında epoksi kullanmanın avantajları arasında yüksek aderans gücü, suya ve kimyasallara karşı direnç, ayrıca yüksek sıcaklık dayanıklılığı sayılabilir. Epoksi aynı zamanda, çatlakların derinliğine göre uygulanabilen çeşitli viskozitelerde mevcuttur, bu da onarımlar sırasında malzemenin çatlaklara derinlemesine nüfuz etmesini sağlar. Ayrıca, epoksi uygulamaları, motor bloğunun malzeme özelliklerini etkilemeden iyileşme sağlar, kaynama, genişleme ve büzülme gibi faktörler göz önünde bulundurularak planlanmaktadır. Bununla birlikte, uygulama